Journey Week 9
- Jayesh Saini
- Oct 7, 2019
- 2 min read
Updated: Feb 6, 2020
In this week I learnt in depth about servo motor under positioning control. Servo motor or servo is a rotary actuator that allows for precise control of angular position, velocity and acceleration. Servos are used to manage movement of joints, pan and tilt and continuous rotational movement. EZ-B sends an electrical signal that tells the servo what position to reach and how quickly to get there. There is another terminology in servo mechanism known as PWM (Pulse Width Modulation) which is a process of turning ON and OFF digital voltage quickly to simulate a range of voltage. We can use PWM to vary the brightness of an LED, for example servo uses PWM as well (PWM standard = 20 ms [frame of a servo PWM signal]). So, now the question arises how servo works? There is a simple way to answer that question, heart of a servo is a small direct current (DC) motor. These motors run on electricity from a battery and spin at high RPM (rotations per minute) but put out very low torque (how much power servo has, avg. more than 2-3 kg/cm@5 volts) i.e., a twisting force used to do work-we apply torque when you open a jar. An arrangement of gears takes the high speed of the motor and slows it down while at the same time increasing the torque. A servo designed to provide more torque for heavier work, the gears are made of metal and are harder to damage such as EZ-Robot servos. In a servo, a positional sensor on the final gear is connected to a small circuit board. The sensor tells this circuit board how far the servo output shaft has rotated. The electronic input signal from the computer also feeds into that circuit board. The electronics on the circuit board decode the signals to determine how far the user wants the servo to rotate. It then compares the desired position to the actual position and decides which direction to rotate the shaft so it gets to the desired position.
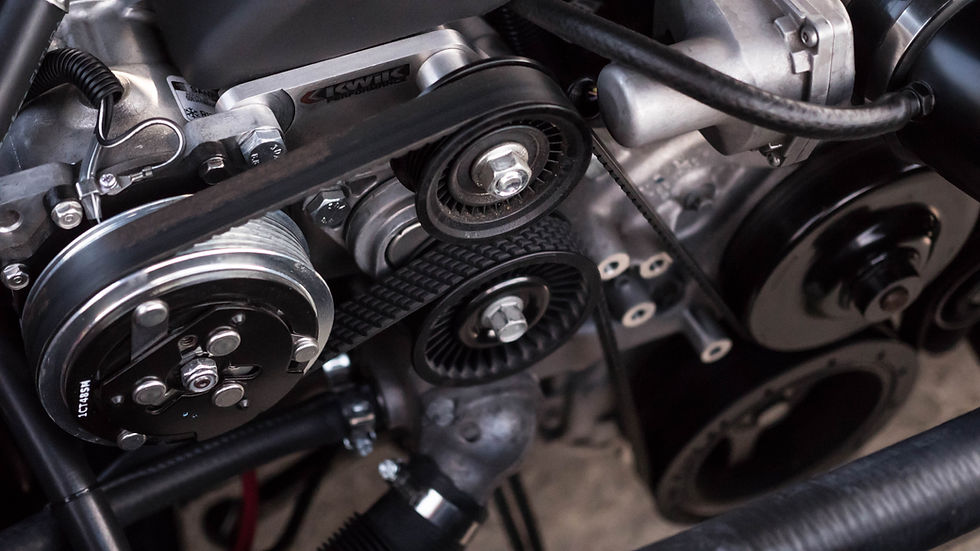
Comments